Bonding WPS for Beginners: Starting with Welding Procedure Requirements
Opening the Power of Welding WPS: Methods for Performance and Safety in Manufacture
In the realm of fabrication, Welding Treatment Specs (WPS) stand as the backbone of welding procedures, dictating the essential steps for accomplishing both efficiency and safety and security in the manufacture process. Comprehending the complexities of WPS is critical to harnessing its complete possibility, yet lots of companies struggle to unlock truth power that lies within these records (welding WPS). By delving right into the strategies that maximize welding WPS, a world of improved productivity and enhanced security awaits those ready to discover the nuances of this essential aspect of fabrication

Value of Welding WPS
The significance of Welding Procedure Requirements (WPS) in the fabrication market can not be overemphasized. WPS offer as a crucial roadmap that describes the required steps to make certain welds are done regularly and appropriately. By defining vital specifications such as welding procedures, products, joint layouts, preheat temperature levels, interpass temperature levels, filler metals, and post-weld heat treatment demands, WPS give a standard approach to welding that enhances efficiency, top quality, and safety and security in manufacture processes.
Adherence to WPS helps in achieving uniformity in weld high quality, minimizing the chance of problems or structural failures. This standardization likewise helps with conformity with market guidelines and codes, ensuring that produced frameworks fulfill the needed safety and security criteria. Additionally, WPS documentation enables welders to replicate successful welding treatments, resulting in constant results throughout different jobs.
In significance, the meticulous development and strict adherence to Welding Procedure Requirements are paramount for maintaining the honesty of welded structures, securing versus prospective risks, and upholding the credibility of construction business for delivering high-quality product or services.
Key Aspects of Welding WPS
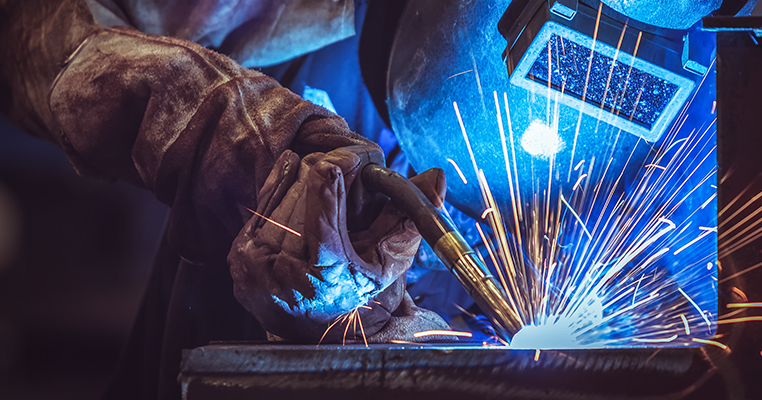
Enhancing Effectiveness With WPS
When maximizing welding procedures, leveraging the crucial elements outlined in Welding Procedure Specs (WPS) comes to be important for streamlining processes and making the most of productivity. One way to improve effectiveness with WPS is by carefully choosing the ideal welding specifications. By adhering to the particular guidelines provided in the WPS, welders can ensure that the welding equipment is set up appropriately, leading to constant and high-grade welds. Additionally, complying with the pre-approved welding series detailed in the WPS can considerably lower the time spent on each weld, eventually boosting overall efficiency.
In addition, appropriate training and certification of welders in understanding and applying WPS can additionally improve effectiveness. Guaranteeing that all employee are skilled in interpreting and performing the WPS accurately can minimize errors and rework, saving both time and sources. Frequently assessing and upgrading the WPS to incorporate any kind of lessons discovered or technical improvements can additionally contribute to performance renovations in welding procedures. By embracing the standards stated in the WPS and continually seeking methods to maximize procedures, fabricators can attain greater efficiency degrees and exceptional end results.
Ensuring Safety in Manufacture
:max_bytes(150000):strip_icc()/MIG20welding20arc20in20action-2000-e8844d72f5094d408b5ab6f1c9436a4f.jpg)
Guaranteeing safety and security in construction includes a diverse approach that incorporates numerous elements of the welding procedure. Welders need to be equipped with proper gear such as safety helmets, gloves, and safety clothing to alleviate risks linked with welding tasks.
Moreover, adherence to correct ventilation and fume removal systems is vital in preserving a healthy and balanced workplace. Welding fumes have damaging materials that, if breathed in, can posture significant wellness threats. Applying effective ventilation actions assists to minimize exposure to these hazardous fumes, advertising respiratory health among workers.
Routine tools upkeep and inspections are likewise crucial for ensuring security in manufacture. Faulty machinery can result in crashes and injuries, emphasizing the importance of regular checks and prompt repair work. By focusing on safety discover this measures and promoting a culture of understanding, manufacture centers can develop a efficient and protected work atmosphere for their employees.
Implementing WPS Best Practices
To improve operational efficiency and ensure high quality results in fabrication procedures, including Welding Procedure Requirements (WPS) ideal techniques is paramount - welding WPS. Executing WPS finest methods includes precise preparation, adherence to industry standards, and continuous monitoring to guarantee optimal outcomes. First of all, choosing the appropriate welding procedure, filler material, and preheat temperature defined in the WPS is crucial for achieving the preferred weld quality. Secondly, making sure that certified welders with the needed accreditations perform the welding treatments according to the WPS guidelines is vital for consistency and dependability. Frequently updating and reviewing WPS documents to mirror any kind of procedure enhancements or modifications in materials is also a vital ideal practice to keep accuracy and significance. Furthermore, providing comprehensive training to welding employees on WPS demands and finest methods cultivates a culture of her comment is here safety and security and high quality within the construction setting. By vigilantly carrying out WPS best methods, fabricators can enhance their operations, lessen errors, and provide remarkable products to fulfill client expectations.
Final Thought
Finally, welding WPS plays an important duty in ensuring effectiveness and safety in fabrication procedures. By focusing on crucial elements, enhancing efficiency, and executing ideal practices, companies can optimize their welding operations. It is necessary to focus on precaution to stop mishaps and make certain a smooth manufacturing procedure. By following these strategies, services can open the complete possibility of welding WPS in their fabrication operations.
In the realm of construction, Welding Procedure Specifications (WPS) stand as the backbone of welding operations, dictating the required steps for accomplishing both efficiency and safety in the fabrication process. By defining essential parameters such address as welding processes, products, joint styles, preheat temperatures, interpass temperatures, filler metals, and post-weld warmth therapy demands, WPS offer a standardized approach to welding that enhances performance, top quality, and safety and security in construction processes.
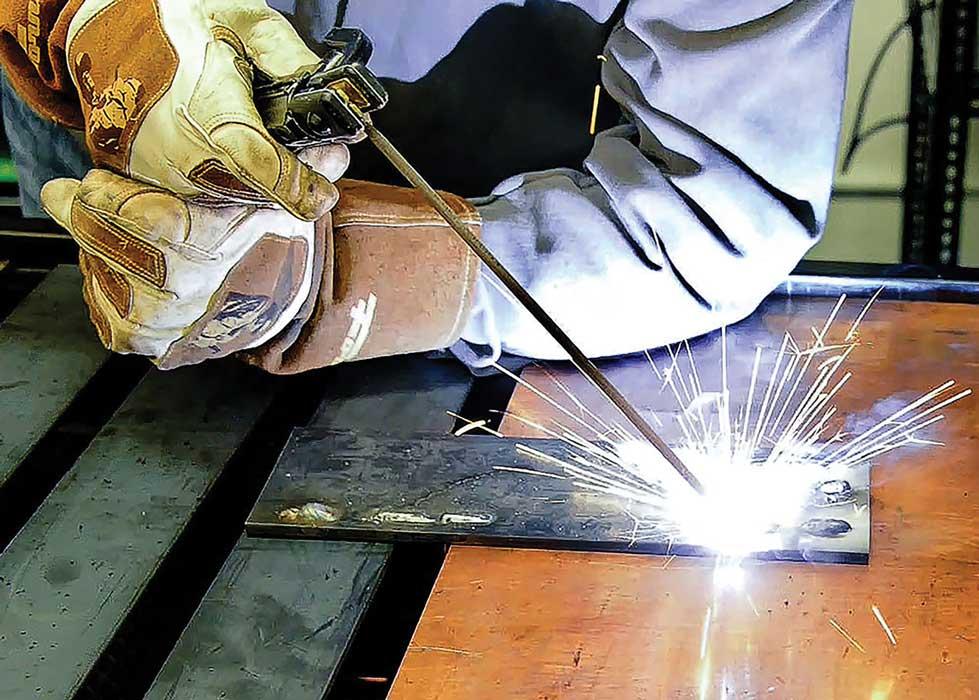
When enhancing welding procedures, leveraging the vital elements described in Welding Procedure Requirements (WPS) becomes important for enhancing procedures and making best use of productivity. (welding WPS)